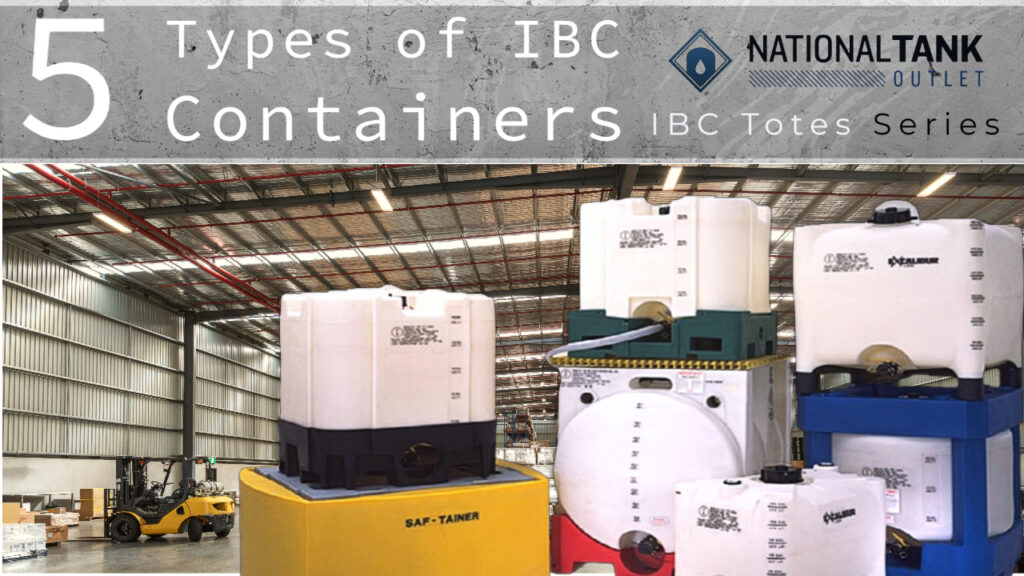
Intermediate bulk containers (IBCs, IBC totes, pallet tanks) are available in various model types, manufacturing materials and storage volumes to suit a wide range of work uses, scenarios, and conditions. Across company and industry sectors, there are five main types of IBCs that are commonly chosen for specific work cases. They include water, chemical, oil and gas, diesel exhaust fluid (DEF) and food grade IBCs.
The engineering and design standards of these IBC types provide a highly effective and efficient alternative to similar portable containers and are easier to handle, safer to use, and overall more resourceful.
Manufacturing, Engineering, and Advantages
The five IBC types are manufactured from durable metal alloys, industrial strength plastic or are a composite of the two materials. The various IBC containers provide significant resistance to application stress and commodity corrosion. IBCs are standardized according to governmental law codes and independent authorities to provide a consistent, reliable, and versatile cargo tank that is, often times, long-term reusable.
The advantages of an IBC’s engineering contribute to every facet of container use when it comes to shipping, logistics, labor, cargo security, loss of product, disposal and potential liability concerns. Considering these advantages, it can perhaps be easily understood why companies look to these 5 types of IBC containers as go-to choices for their applications and handling of business commodities.
Water IBCs
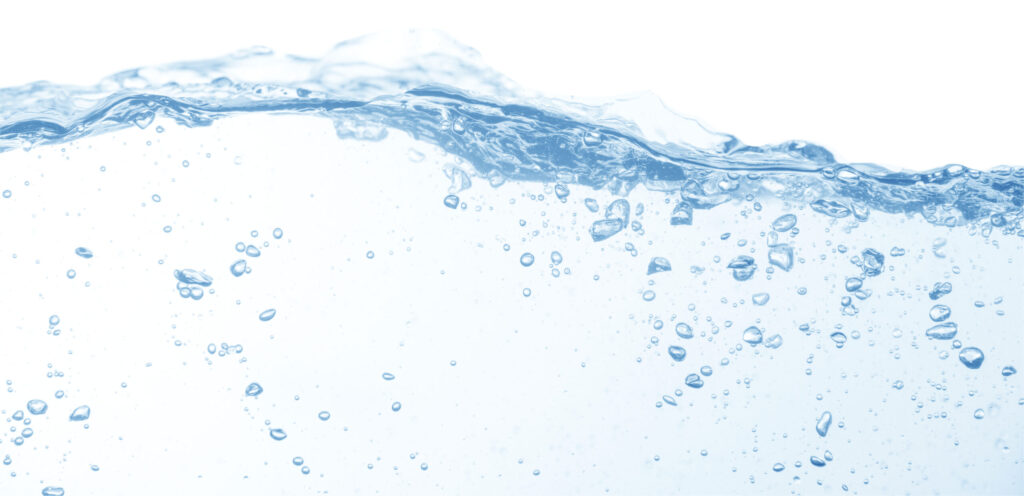
Water IBCs are the most used IBC type and specifically includes the well-known poly caged tote, also called a composite IBC. Water IBCs are both standardized and certified for use with: pure, potable drinking water, non-potable water, water used for production or processes, to handle wastewater, as well as in rainwater and aquaponic water systems. Common industries that use Water IBCs include agriculture, manufacturing of goods and chemicals, aquaculture, construction, water hauling, pharmaceutics, healthcare, energy development, landscaping, power washing, cleaning, and detailing.
When considering the material and design standards of IBC totes, all IBCs are ANSI/NSF 61 approved for potable water, (excluding reconditioned totes), but the caged IBC tote has the most cost-effective purchase price and engineering for water handling. Caged IBCs are made using virgin HDPE resin that meets FDA, ANSI, NSF quality requirements for water and consumable-based contact, are UV stabilized and are UN/DOT 31HA1/Y approved with shipping permits and labels.
Composite IBC totes feature a reinforced, warp-resistant steel grid that contains the inner high-density polyethylene (HDPE) bottle. The inner tote bottle is extrusion blow-mold manufactured to either a 275 gallon or 330 gallon capacity tank. Water IBCs feature a 6” diameter top inlet screw cap and 2” drain ball valve with quick disconnect camlock coupler for easy connections and control of product flow.
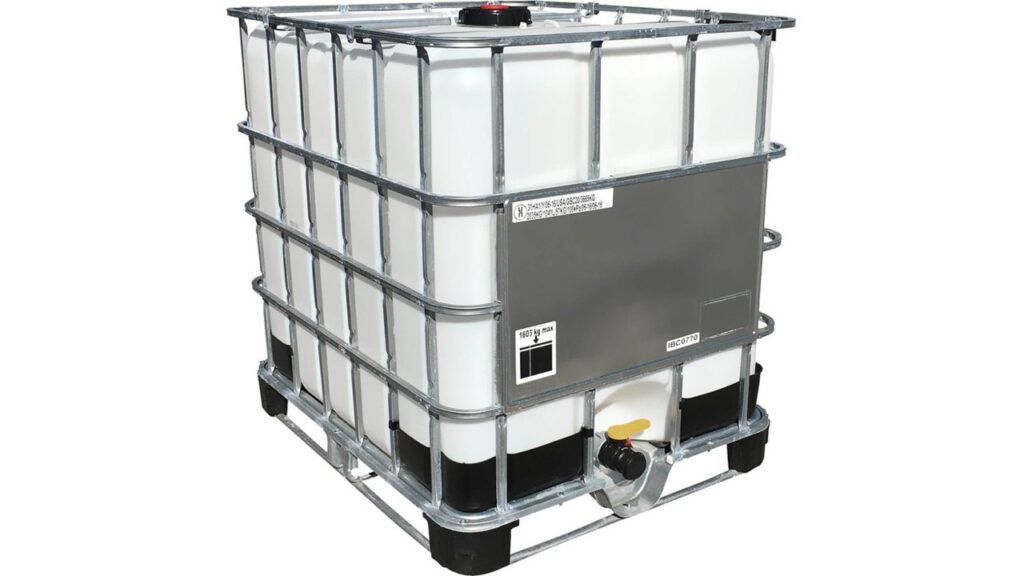
The totes are cube shaped, can be stacked up to four high when empty, and have four-way forklift, pallet jack channels that collectively provides full access handling and intuitive spatial organization. Water IBCs are not recommended to be stacked more than two high when full.
The CageBuster IBC tote is a recent product innovation by Snyder Industries engineered to be a more durable, longer lasting alternative to the caged IBC tote.
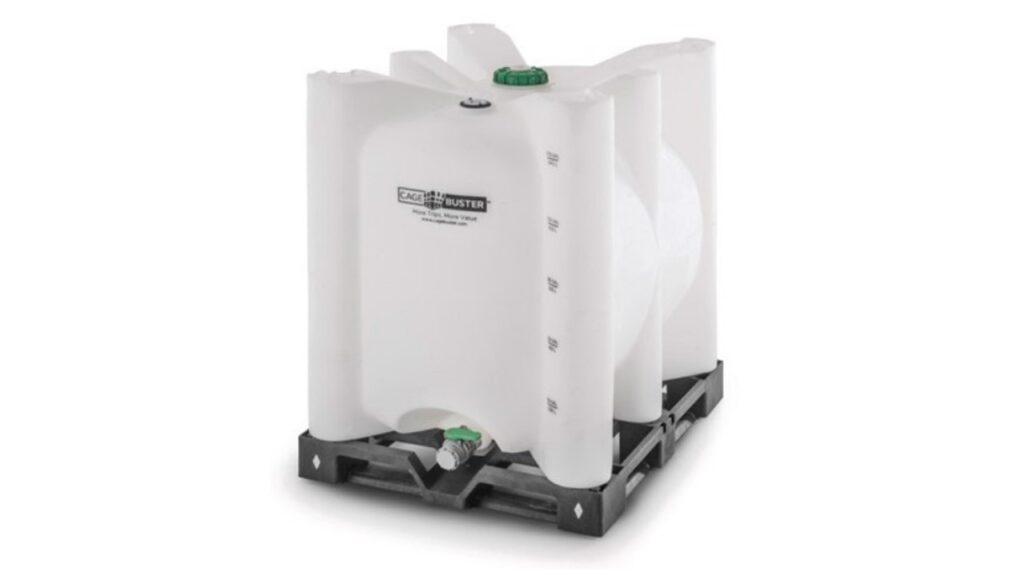
The Water IBC caged tote is the most well-known of all IBC types and the one popularly used by do-it-yourself individuals and hobbyists for rainwater harvesting, backyard aquaponics, hydroponics, gardening, and other intuitive homemade projects.
Chemical IBCs
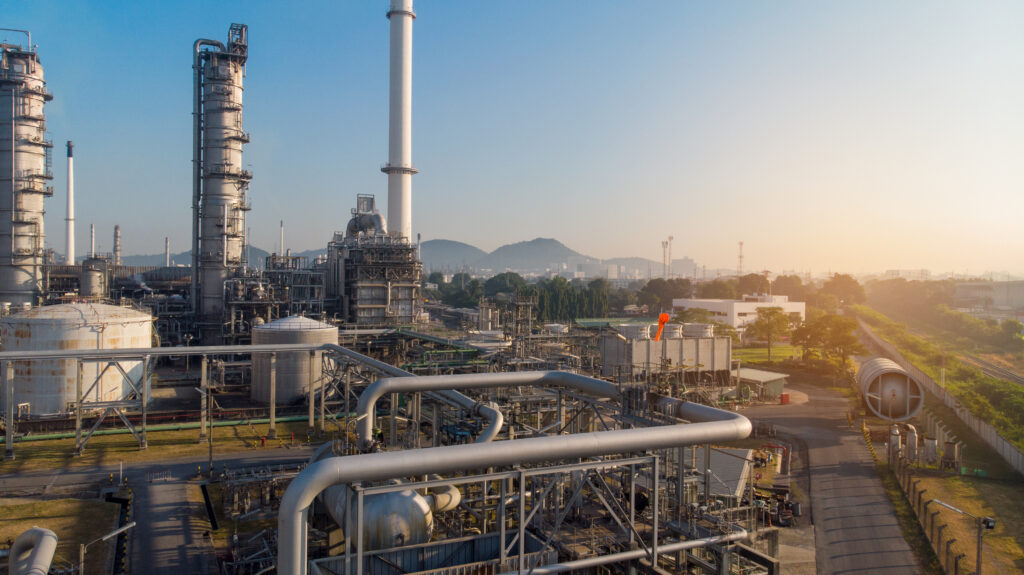
Chemical IBCs are portable, multi-purpose, full-application cargo tanks specifically manufactured for the safe handling of many chemical commodities. Most Chemical IBCs are rated for use with liquids up to 1.9 specific gravity and are made from chemically resistant materials and components.
Material options for Chemical IBCs include either high density polyethylene (HDPE) plastic made with ½” thick sidewalls or the durability of stainless steel or carbon steel metal. Standard gasket options include EPDM, Viton, or Teflon. Fittings, valves and outlet adaptor options range in style and are available made from polypropylene, PVC, CPVC, or stainless steel.
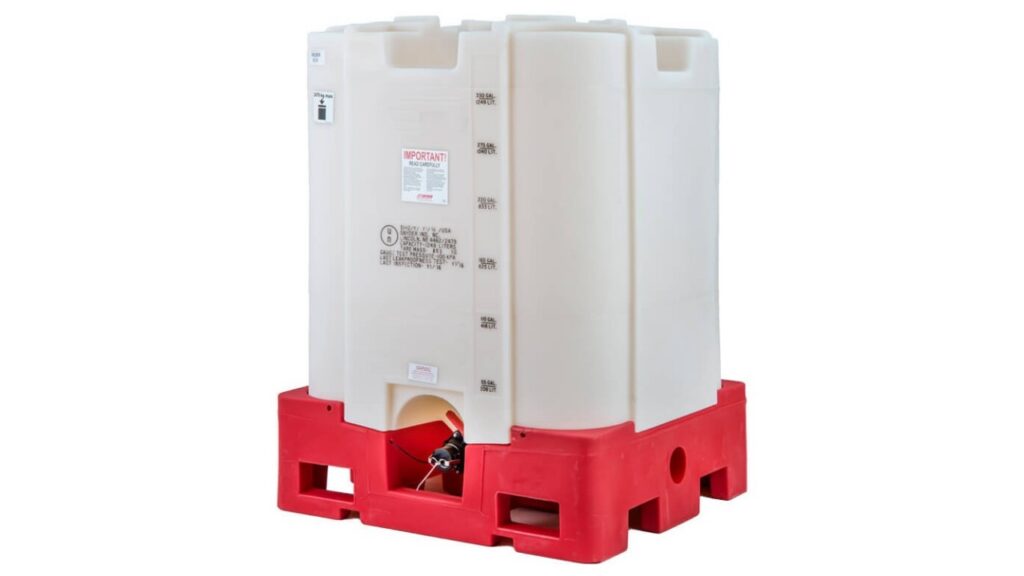
A Chemical IBC has been engineered to meet or exceed the certification standards necessary per Title 49 CFR that approve the containers for UN/DOT handling and transit of many chemical liquids, semisolids, and granulated solids in full consideration of potential chemical activity, reactions, intrinsic properties, and vapor environments.
Substances that are corrosive, prone to external reactions, or sensitive to contamination are capable of long-term, consistent handling in a Chemical IBC tote. Common chemicals compatible and often transported in IBCs include strong acids such as hydrochloric acid, caustics like sodium hydroxide, and the various classes of oxidizers, chlorites, solvents, degreasers, surfactants, process intermediates, and semi-volatile chemicals.
Common Chemical IBC types include:
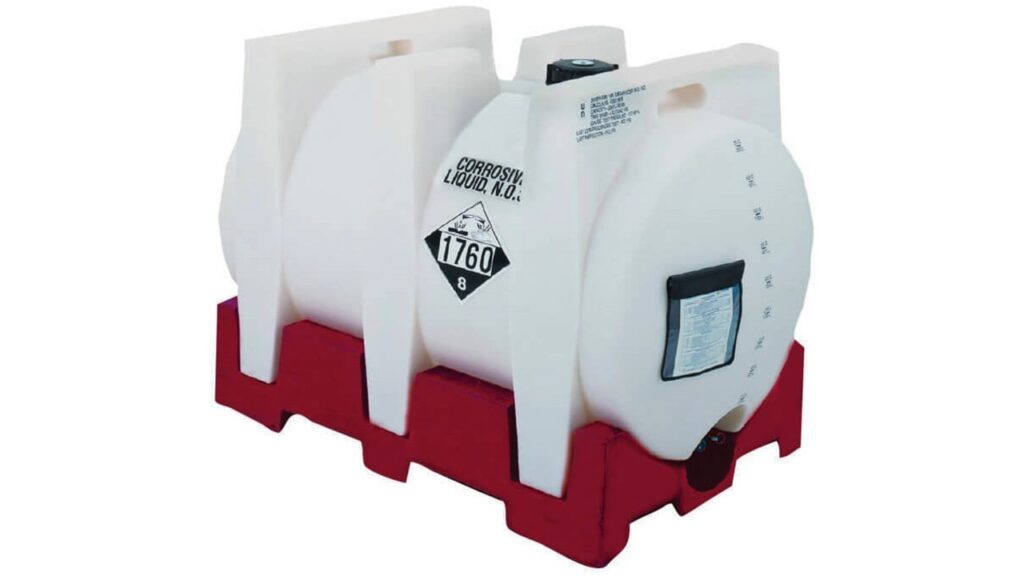
All Chemical IBC models are UN/DOT approved shipping containers with permit labels. Most Chemical IBCs feature a sloped tank bottom angled to either 30° or 45° to promote the complete delivery of the internal cargo.
Chemical IBC containers feature a self-regulating relief vent (or vents) designed to function automatically at certain pressure thresholds. Automatic relief vents allow Chemical IBC totes to withstand internal pressures up to 15 psi (100 kPa). On request, Ultratainer IBCs can be specially designed to withstand increased internal pressures up to 62 psi (428 kPa) as necessary.
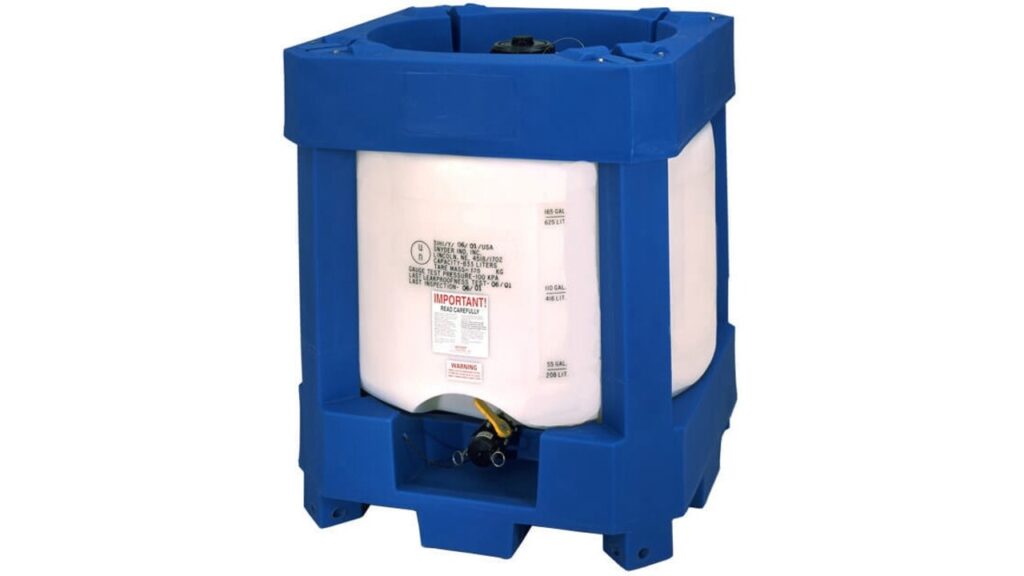
With a Chemical IBC tote, chemicals can be safely, conveniently stored, handled and integrated into applications with limited risk to safety and waste of materials.
Oil and Gas IBCs
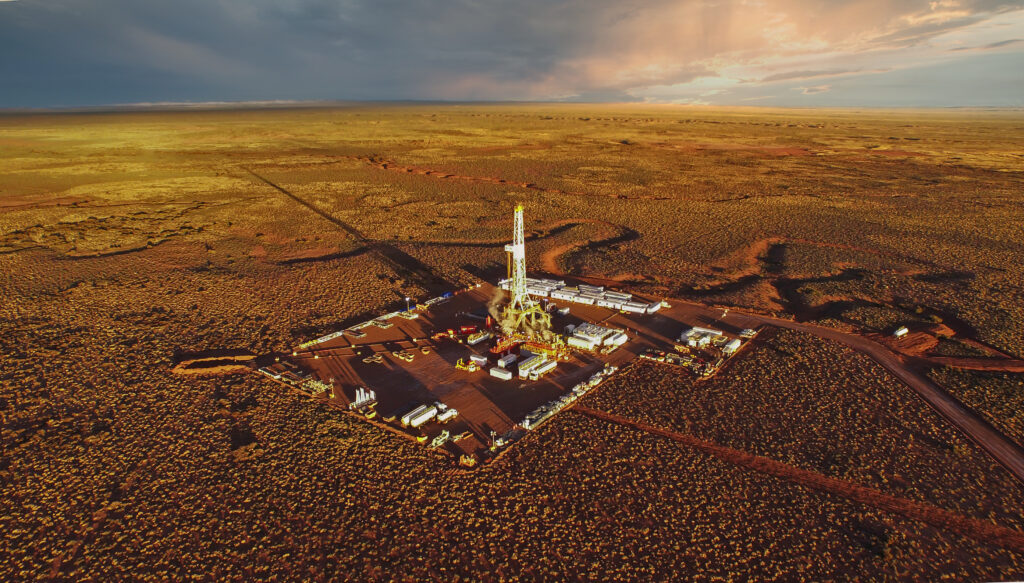
Oil and Gas IBCs are intermediate bulk containers approved for scenarios involving petroleum resources and petrochemical industry applications. Stainless Steel and Carbon Steel are the most used IBC tank types for these harsh, chemically demanding and corrosive environments.
Oil and Gas tote types are often used to contain, store & distribute natural raw oil, liquids intended for refinery and production, application chemicals, as well as refined fuel products, intermediates, or waste materials associated with modern combustible fuels.
Metal Oil and Gas IBCs are approved per UN/DOT and IMDG handling requirements, meet UL 142, ASME pressure standards and NFPA 30 fire codes for up to Class IB combustibles. The tanks feature large 22” bolt-and-clamp manways, stainless steel outlet valves, top-located lifting lug eyelets, and 3-way fork access.
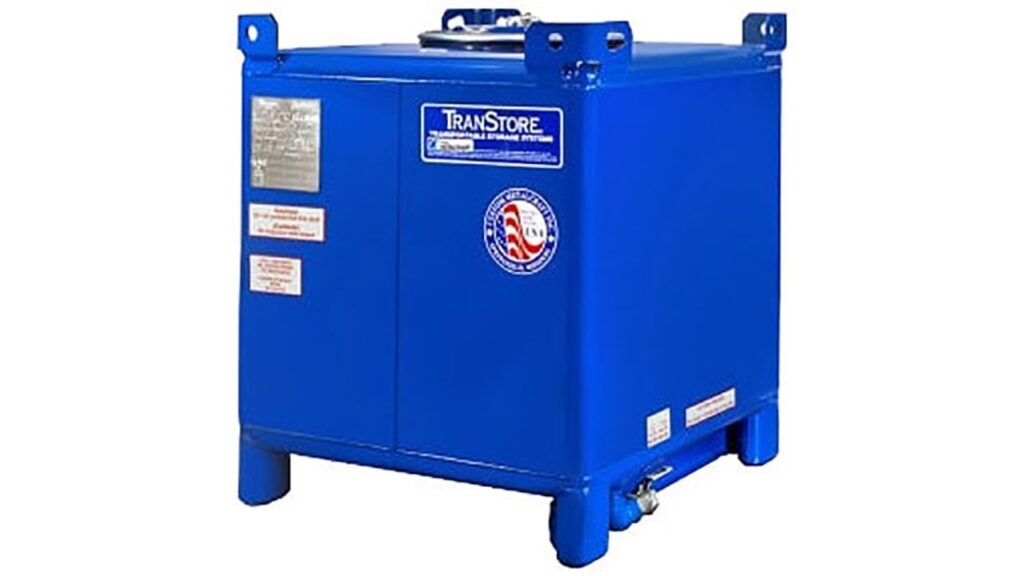
Oil and Gas totes have been approved for their extensive use within oil well fields, offshore ocean platforms, drilling, refining and the handling of petroleum-based commodities.
DEF IBCs
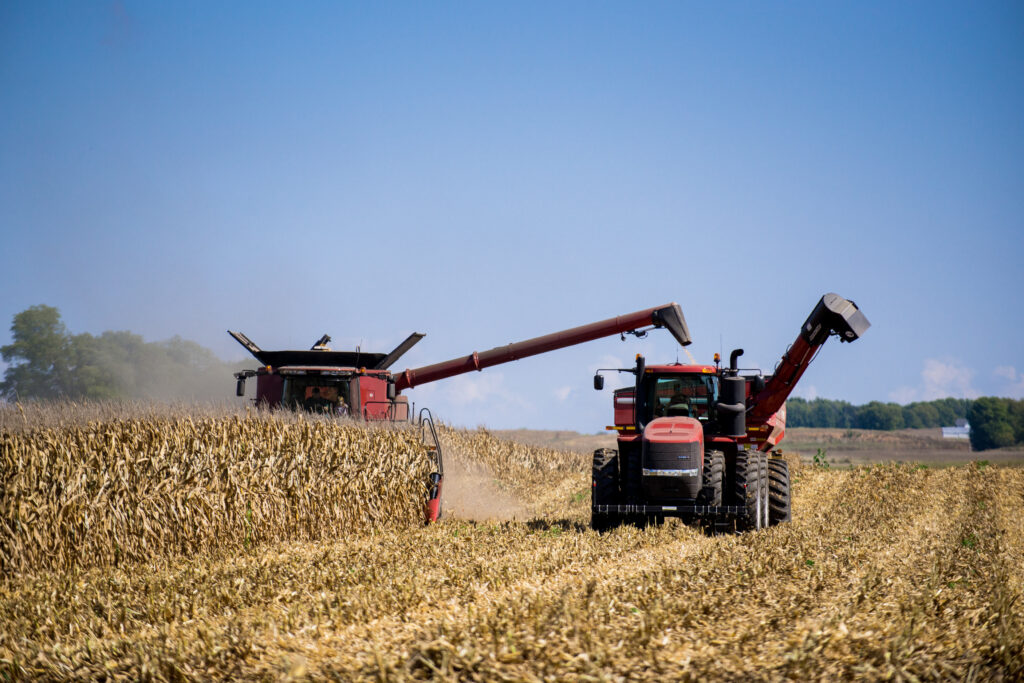
DEF IBC totes are intermediate bulk containers built with special equipment for the safe, pure handling of Diesel Exhaust Fluid (DEF) per ISO 22241-3.
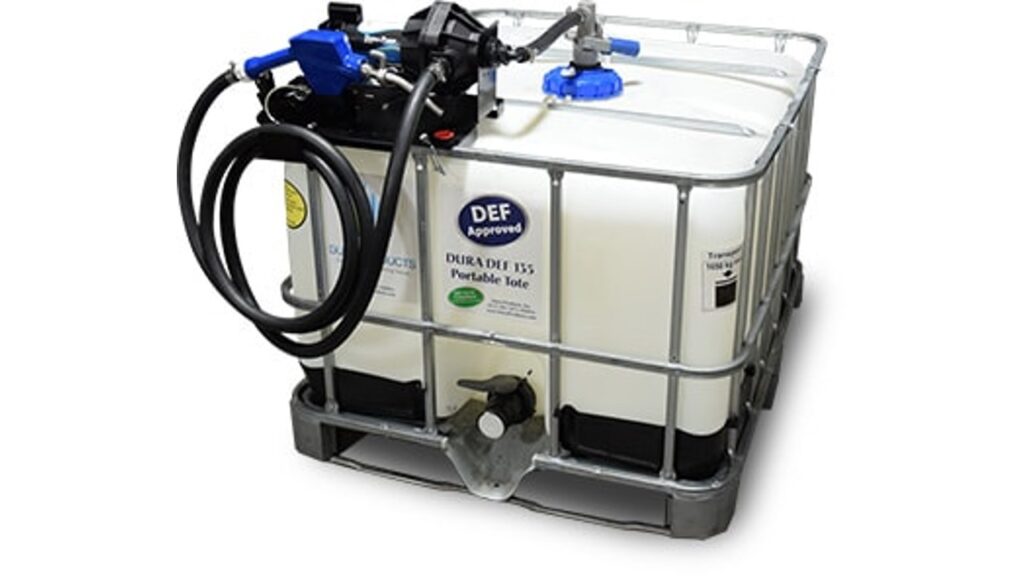
DEF, also known as Aqueous Urea Solution 32 (AUS 32; Transit DEF) or AUS 40 (Marine DEF), is a regulated chemical commodity similar to motor fuel that has strict purity requirements concerning its transfer and use.
DEF IBCs and their associated dispensing equipment guarantee the standardized handling, storage and use of DEF solutions to prevent contamination, crystallization, and/or pump cavitation. DEF IBC totes are seamlessly molded using industrial strength HDPE with UV stabilizers and are fabricated from high quality materials and components certified per ANSI, NSF, ISO, CFR, and the FDA for DEF solutions.
DEF tote capacities range from 135 gallons up to 330 gallons and feature dispensing systems in either 12V or 120V voltages to match individual work case needs. With the proper care, use, and maintenance, DEF IBC totes can be used many times in the handling of diesel exhaust fluid.
Food Grade IBCs
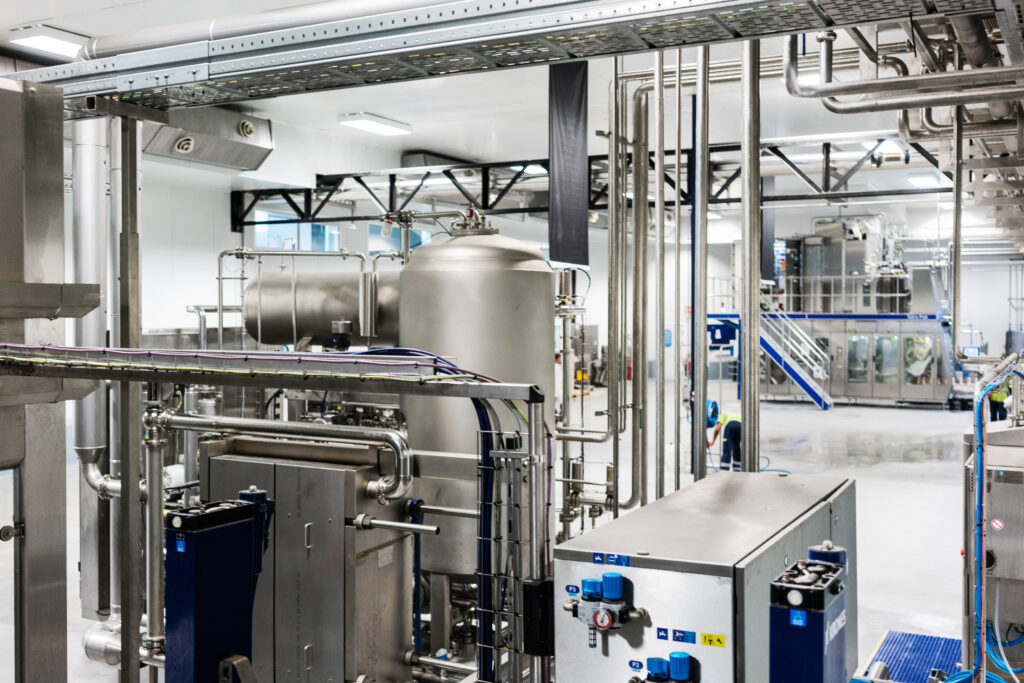
Food Grade IBC containers are manufactured so all the tote’s materials, components and fittings meet U.S. FDA and Title 21 CFR requirements for the handling and long-term contact with commodities intended as food or beverage ingredients and for consumption.
The most common food grade IBC chosen for use are Stainless Steel IBC tanks due to their extensive cleanliness and hygiene capability, ingredient compatibility, the purity of their 10 gauge 304/316 stainless steel construction, and their large 22” diameter inlet port that allows for interior access, easy filling, cleaning, product mixing as well as evaluating the integrity of extended storage commodities.
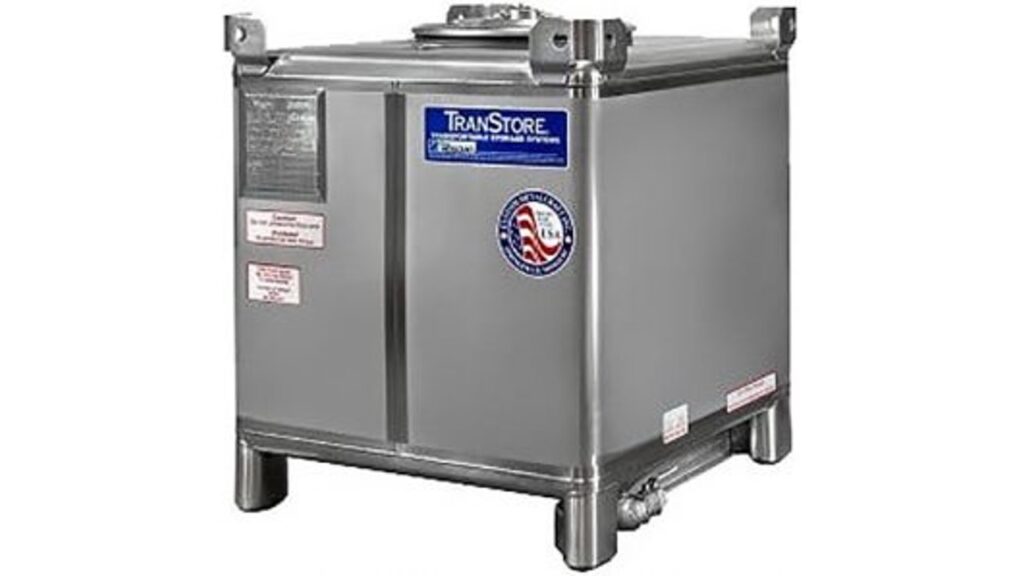
Food grade IBCs provide discharge tap valves for hose and transfer attachments to move internal cargo without ever leaving a contained, clean environment. They are compatible with a wide range of consumer-end based solid to liquid product fluids, powders, granules, food oils and syrups, which includes nuts, grains, dairy, corn products, and sugar to name a few examples.
Food grade IBCs are frequently used within food production and transport scenarios as well as winery vineyards and breweries in extended age-storage, fermentation, distillation, as well as the blending of company products.
Takeaway | 5 Types of IBC Containers
Whenever needing to transport, store, or distribute an intermediate volume of cargo, there is most likely an intermediate bulk container ideally manufactured, engineered, and certified for the job. We are a leading provider and authority for the industry’s top available choices in intermediate bulk containers built in the USA and manufactured by North America’s leading IBC manufacturers Snyder Industries and Custom Metalcraft.
For any questions, comments or requests, contact us by phone, email, send us a message or use our live chat option today.